DESCRIPTION
CARTRIDGE FOR MOISTURE-CURABLE SEALANT
Technical Field [0001] This invention relates to a cartridge for use with a moisture-curable sealant (referred to below as a moisture-curable sealant cartridge) that exhibits an improved moisture barrier performance. The invention also relates to the aforesaid cartridge -filled with a moisture-curable sealant and a method for making the aforesaid cartridge.
Background Art [0002] A wide range of cartridges for holding and storing moisture-curable sealants have been proposed, for example in Japanese Publication of Examined Utility Model Application Number Hei 3-28941 (28,941/1991) there is provided a cartridge in which an end member is disposed at and closes one end of a cylindrical cartridge body, a nozzle-equipped discharge member is disposed in the center of this end member, the exit port in the discharge member is sealed by a moisture-proof film, and an extrusion plunger is slidably engaged in the other end of said cartridge body.
[0003] The use of polyolefin resins, such as polyethylene or polypropylene, and aluminium (Al) foil-laminated thick paper (JP Kokai 2001-240154) as cartridge body materials is known. However, spent cartridges using Al foil-laminated thick paper as the cartridge body are unsuitable for disposal as industrial waste by incineration and cartridges made from polyolefin resins, such as polyethylene or polypropylene, are known to suffer from inadequate moisture barrier performance.
[0004] Depending on the particular type of moisture-curable sealant contained in the cartridge, the moisture that permeates through the cross section of the cartridge body during long-term storage can cause problems including partial curing and, in cases when the substrate to which sealant is applied e.g., glass sheet, metal sheet, or metal sash, is being maintained at a high temperature at the time of sealant application, the production of bubbles in the sealant material is likely to occur at the interface between the substrate and the sealant. [0005] The use of inner coatings between the body of a cartridge and the outer surface of the related plunger have been described in, for example, JP Kokai S63-27584 which describes the use of a two component composition comprising:-
(i) from 90 to 10(wt)% of a wax having a melting point (m.p.) of preferably > 45°C; and (ii) from 10 to 90% of polybutene or polyisobutylene as a sealing agent for sealing between the inner peripheral surface of the cylindrical main body of a cartridge and the outer peripheral surface of a plunger slidably fit in the cylindrical main body.
[0006] JP Kokai Hei 11-321895 and JP Kokai Hei 11-321896 describe a synthetic-resin- made tubular container for e.g. storing cosmetics. The container is made using the following steps :-
1. A cylindrical primary molding is molded by injection molding with polyester resin-based synthetic resin. 2. A secondary molding having a body, a shoulder, and a neck integrally is molded from the cylindrical primary molding by biaxially orientation blow molding procedure. 3. The secondary molding is coated with an epoxy resin.
In the description of the both applications, an epoxy resin is combined with a solvent and coated by dipping, spraying or printing and cured by heating. The epoxy resin is an oligomer resin, preferably a glycidyl ether or glycidyl ester type.
Disclosure of Invention [0007] The object of this invention is to solve the problems identified above in the prior art by providing a moisture-curable sealant cartridge that exhibits an excellent moisture barrier performance and thereby enables the long-term storage of moisture-curable sealant contained therein.
[0008] hi accordance with the present invention there is provided a moisture-curable sealant cartridge comprising a cylindrical polyolefin cartridge body having at one end thereof a polyolefin end member with an exit port and at the other end an opening sized to receive a slidably engageable extrusion plunger, characterized in that an electromagnetic radiation-curable epoxy compound-based composition is coated and cured onto at least that portion of the cartridge body, which in use will encompass moisture-curable sealant held in the cartridge. It is preferable that the moisture-curable sealant cartridge additionally comprises a slidably engageable extrusion plunger received in the opening.
[0009] This invention additionally relates to a moisture-curable sealant cartridge filled with a moisture-curable sealant comprising the aforesaid moisture-curable sealant cartridge, a slidably engageable extrusion plunger received in the opening, and a moisture-curable sealant filled in the body of the aforesaid cartridge and to a method for producing moisture- curable sealant cartridge bodies characterized by coating an electromagnetic radiation- curable epoxy compound-based composition on the aforesaid cartridge body and thereafter curing the electromagnetic radiation-curable epoxy compound-based composition by exposure to radiated active energy.
[0010] The cartridge body and end member are preferably molded as a single unit made from a polyolefin. The extrusion plunger may be made from any suitable material such as for example a thermoplastic resin, a polyolefin or metal although the use of polyolefin is preferred. Any suitable polyolefin may be used, for example, high-density polyethylene, low-density polyethylene, polypropylene, and ethylene-propylene copolymer. High-density polyethylene is particularly preferred.
[0011] Any suitable method for molding the cartridge body, end member, discharge member, and extrusion plunger may be used. For example, the discharge member, end member, and cartridge body may be integrally molded by injection molding. Alternatively the end member may be made by injection molding, and the cylindrical cartridge body may be made by extrusion molding, and then the resulting components may be melt-bonded to each other.
[0012] Preferably the end member comprises a discharge member which forms a discharge channel from the exit port. The discharge member may be in the form of a nozzle or more preferably is releasably interengageable with a nozzle in view of the advantages this affords with regard to storage and transport of the cartridge. The discharge channel may be sealed prior to use but in use, once the seal has been removed or broken, is adapted to guide sealant being dispensed from the cartridge body into the nozzle for application onto a substrate. [0013] The thickness of each of the cartridge body, end member, and extrusion plunger is individually preferably in the range of from 0.7 to 2.5 mm. A thickness below the lower limit of this range results in problems such as an inadequate cartridge strength and unacceptable moisture barrier performance. A thickness above the upper limit on the given range causes problems such as poor economics and a reduction in workability due to the increased weight.
[0014] A moisture proof film preferably seals the exit port of the discharge member that is disposed in the center of the end member. This moisture proof film may be of any suitable type but preferably comprises a laminate of a metal foil, such as aluminum, with a hot-melt adhesive in which case the exit port is preferably sealed by melt-bonding the hot-melt adhesive side of the moisture proof film over the inner surface of the discharge member.
[0015] In use sealing is preferably carried out by first filling the cartridge body with moisture-curable sealant and then inserting the extrusion plunger. The seals on the exit port and where present the discharge member are then broken or removed, where required a nozzle is engaged on the discharge member. Pressure is then applied on the extrusion plunger forcing sealant to travel through the exit port, discharge member and where present nozzle for application onto the target substrate.
[0016] Preferably a layer of hydrophobic sealant is provided on at least the region of the inner wall surface of the cartridge body that is in contact with the extrusion plunger. Any suitable hydrophobic sealant may be utilized such as for example long-chain alkyl-modified polysiloxane; waxes such as paraffin wax, microcrystalline wax, vegetable waxes, animal waxes, and polyethylene waxes; or a mixture of such waxes with polybutene or polyisobutylene.
[0017] The moisture-curable sealant cartridge of the type described above is already known for retaining moisture-curable sealants. However, in the present invention an electromagnetic radiation-curable epoxy compound-based composition is coated and cured on at least that portion of the cartridge body that, in use encompasses or holds moisture- curable sealant. The resulting cured coating is adapted to prevent the ingress of atmospheric moisture into the cartridge interior by preventing the permeation of atmospheric moisture through the cartridge body. This enables long-term storage of moisture-curable sealant held therein. The electromagnetic radiation-curable epoxy compound-based composition may be coated and cured over the entire outer surface and/or the entire internal surface of the cartridge body and may also be coated over all or part of the end member. However, the electromagnetic radiation-curable epoxy compound-based composition must be coated and cured on at least that portion of the outer surface and/or internal surface of the cartridge body that encompasses or holds the moisture-curable sealant.
[0018] The electromagnetic radiation-curable epoxy compound-based composition preferably contains an epoxy compound as a base resin. A cross-linking reaction within the composition is induced by exposure to electromagnetic radiation, resulting in the formation of a cured coating. The electromagnetic radiation-curable epoxy compound-based composition is preferably a liquid at room temperature and preferably does not contain solvent. The use of one or more solvents may result in the cartridge having an inadequate moisture barrier performance. This is due to such factors as the generation of pinholes in the coating originating from solvent removal after the application step and the formation of residual microscopic bubbles in the coating, etc.
[0019] Any suitable compounds having epoxy-functional groups or epoxy resins can be used, for example, aliphatic epoxy compounds such as alicyclic epoxy-functional monomers, alicyclic epoxy resins, and polyglycidyl ether monomers from aliphatic polyhydric alcohols and their alkylene oxide adducts, as well as aromatic epoxy compounds such as aromatic epoxy-functional monomers, phenol novolac-type epoxy resins, cresol novolac-type epoxy resins, and bisphenol-type epoxy resins. These epoxy-functional monomers, epoxy oligomers and/or epoxy resins can be used individually or as mixtures as required. Similarly epoxy-functional monomers, oligomers, and/or polymers that have been modified by a radically-polymerizable functional group, such as acryl- and methacryl-modified epoxy resins, as well as various epoxy-modified monomers, oligomers, and polymers such as, for example, epoxy-modified polybutadiene and epoxy-modified acrylic and methacrylic resins may be used. Bisphenol-type epoxy resins are particularly preferred because of their adhesive properties in relation to polyolefins and because they are readily available. [0020] The electromagnetic radiation-curable epoxy compound-based composition preferably contains, in addition to the epoxy compound as described above, photopolymerization initiators, most preferably cationic photopolymerization initiators when ultraviolet radiation is used as the electromagnetic radiation for inducing cure of the composition. Cationic photopolymerization initiators are compounds that upon exposure to, for example, ultraviolet radiation, release a substance that can initiate cationic polymerization and thereby induce crosslinking of the aforesaid epoxy compounds. The photopolymerization initiator may alternatively be a radical photopolymerization initiator. Radical photopolymerization initiators are compounds that upon exposure to, for example, ultraviolet radiation, release a substance that can initiate radical polymerization and can thereby crosslink an acrylic or methacrylic compound that contains at least one unsaturated acryloyl group, h the case of the use of a radical photopolymerization initiator, the electromagnetic radiation-curable epoxy compound-based composition may be exemplified by a composition comprising a radical photopolymerization initiator and a polymerizable monomer comprising an acrylate or methacrylate ester and a polymerizable prepolymer containing an epoxy skeleton, e.g., epoxy acrylate.
[0021] The electromagnetic radiation-curable epoxy compound-based composition used by this invention may contain other additives within a range that does not impair the object of the invention. These additives may for example include viscosity regulators, sagging inhibitors, water resistance agents, dispersants, crosslinkers, gelling agents, antiskinning agents, delustrants, defoamers, color separation inhibitors, antimolds, mist inhibitors, slip agents, antioxidants, drying agents, humectants, waxes, organic pigments, inorganic pigments, moisture-resistant pigments, carbon black, titanium white, metal powders, polymerization accelerators, and polymerization inhibitors capable of preventing the problems of polymerization in the dark and polymerization during storage.
[0022] Commercial electromagnetic radiation-curable epoxy compound-based inks, paints, and coatings are well-suited for use as the electromagnetic radiation-curable epoxy compound-based composition under consideration. For example, FDSS46 and FDSS210 from Toyo Ink Mfg. Co., Ltd., UN POL from Teikoku Printing Inks Mfg. Co., Ltd., and Series 9076 Ink from the MARKEM Corporation are well-suited for use as the electromagnetic radiation-curable epoxy compound-based composition. [0023] These electromagnetic radiation-curable epoxy compound-based compositions adhere well to polyolefins such as high-density polyethylene, low-density polyethylene, polypropylene, and ethylene-propylene copolymers, cure rapidly, and provide cured films that exhibit excellent film strength, friction resistance, water resistance, and weathering resistance.
[0024] The electromagnetic radiation-curable epoxy compound-based compositions may be applied onto a cartridge body by any suitable method, such as for example roll coating, offset coating, gravure coating, gravure-offset coating, spray coating, immersion coating, and screen printing. Once the cartridge body has been coated with the composition, the treated cartridge body may be exposed to electromagnetic radiation over its whole surface; alternatively electromagnetic radiation may be irradiated from a single location while the cartridge body is rotated.
[0025] Ultraviolet radiation, x-rays, and electron beams are examples of the electromagnetic radiation that can be used to induce cure of the electromagnetic radiation- curable epoxy compound-based composition. A variety of light sources may be used in the case of cure induction using ultraviolet radiation, such as, for example, pressurized and high- pressure mercury lamps, ultrahigh-pressure mercury lamps, metal halide lamps, gallium lamps, xenon lamps, and carbon arc lamps. Light sources that generate light with a wavelength of 200-500 nm are preferred. The ultraviolet radiation can be used in combination with heat generated by, for example, infrared radiation, far infrared radiation, a hot gas current, or high-frequency radiation. Metal halide lamps are preferred for use as the ultraviolet source because they readily afford strong cured films with a high surface hardness. A variety of emitting devices can be used in the case of electron beam-induced cure, for example, Cockcroft- Walton machines, van de Graaf generators, and resonance transformer devices. The electron beam preferably has an energy of from 50 to 1000 eN and more preferably of from 100 to 300 eN. Ultraviolet radiation is preferred for curing the electromagnetic radiation-curable epoxy compound-based composition because ultraviolet sources are inexpensive and easy to handle. [0026] The cured film thickness afforded by the electromagnetic radiation-curable epoxy compound-based composition should be from 0.1 to 100 μm and is preferably from 1 to 50 μm. The moisture barrier performance will be inadequate below the lower limit of the given range, while exceeding the upper limit on the given range can be disadvantageous from a cost standpoint.
[0027] JIS Z 0208, "Test methods for determination of the water vapor transmission rate of moisture proof packaging", or the MOCON method corresponding to this JIS method may be used to measure the moisture permeability of the cartridge body on which the electromagnetic radiation-curable epoxy compound-based composition has been coated and cured. The moisture permeability of the cartridge body measured in a 40°C/90% RH
2 (relative humidity) ambient is preferably no greater than 0.18 g/m per 24 hrs. When this limit is exceeded, the storage stability will in some cases be unsatisfactory depending on the type of moisture-curable sealant contained in the cartridge.
[0028] The cartridge in accordance with the present invention provides a means for the long-term storage of moisture-curable sealants, e.g., silicone sealants, modified silicone sealants, polyurethane sealants, and polysulfide sealants, by virtue of the electromagnetic radiation-curable epoxy compound-based composition coated and cured on at least that portion of the cartridge body that encompasses or holds the moisture-curable sealant. The moisture-curable silicone sealants may have an alcohol-eliminating, oxime-eliminating, amine-eliminating, ketone-eliminating, or aminoxy-eliminating silicone sealant, but a dramatically prolonged storage life can be obtained in particular when a single-package alcohol-eliminating moisture-curable silicone sealant is stored in the inventive cartridge.
Best Mode for Carrying Out the h ventioh [0029] The present invention will now be described further based on the following examples and drawings in which :- Figure 1 contains a lengthwise section of the moisture-curable sealant cartridge used in the examples of this invention; and
Figure 2 contains a schematic drawing of a section of region C in Figure 1, in which a) illustrates an example in which the electromagnetic radiation-curable epoxy compound-based composition has been coated and cured on the outer surface of the cartridge body in accordance with the present invention, b) illustrates an example in which the electromagnetic radiation-curable epoxy compound-based composition has been coated and cured on the internal surface of the described cartridge body, and c) illustrates an example in which the electromagnetic radiation-curable epoxy compound-based composition has been coated and cured on the outer surface and the internal surface of the described cartridge body.
[0030] In Fig. 1 there is provided a cartridge 1 having a cartridge body la made from a polyolefin having at one end thereof a polyolefin end member lb. Cartridge body 1 a and end member lb are molded as a single body. A discharge member lc is disposed in the center of end member lb. At the other end of the cartridge body la is a freely slidable extrusion plunger 2 which is also made from a polyolefin based material. The thickness of the cartridge body la, end member lb, and extrusion plunger 2 is in the range of from 0.7 mm to 2.5 mm. A moisture proof film 4 is provided to seal the exit port of the discharge member lc. This moisture proof film 4 comprises an aluminium foil/hot melt adhesive laminate such that the exit port is sealed by melt-bonding the hot-melt adhesive side of the moisture proof film 4 over the perimeter of the discharge member lc. A nozzle 3 is preferably attached on the discharge member lc. This nozzle 3 is preferably detachable from the discharge member lc in view of the advantages this affords with regard to storage and transport of the cartridge, but the nozzle 3 can also be integrally formed with the discharge member lc.
[0031] A coating of hydrophobic sealant 5 is provided on that region of the internal surface of the cartridge body la in contact with the outwardly facing surface of the extrusion plunger 2.
[0032] An electromagnetic radiation-curable epoxy compound-based composition 6 is coated and cured on at least that portion of the cartridge body la that encompasses or holds the moisture-curable sealant. The cured product afforded by the electromagnetic radiation- curable epoxy compound-based composition 6 prevents the ingress of atmospheric moisture into the cartridge interior by preventing the permeation of atmospheric moisture through the cartridge body la enabling long-term storage of the moisture-curable sealant A retained therein.
[0033] In use the application of sealant onto a substrate is preferably carried out by first filling cartridge body la with moisture-curable sealant and then inserting extrusion plunger 2. The seal on the exit port 4 is broken or removed and pressure is then applied on the extrusion plunger forcing the sealant to travel through the exit port, discharge member lc and nozzle 3 for application onto the target substrate.
[0034] In order to demonstrate the advantageous effects of this invention, the storage stability of moisture-curable sealant filled in inventive cartridges was evaluated by investigating sealant foaming and the occurrence of cured material in sealant subjected to accelerated ageing. The moisture permeability of the cartridges was investigated at the same time.
[0035] Production of the cartridge bodies
Cartridge bodies la were produced by injection molding using a high-density polyethylene resin (density = 0.96). The wall thickness was 1.2 mm, and one end of cartridge body la was closed off by an end member lb having at its center discharge member lc. The circumference of the exit port of the discharge member lc was sealed from the inside by the melt-bonding thereto of a moisture proof film 4 of an aluminum/hot melt adhesive-laminated film. A tapered nozzle 3 of low-density polyethylene was screwed onto the discharge member lc. At the other end of the cartridge body la, a mixture of polybutene and microcrystalline wax (mixing ratio = 3 : 2) was coated over the internal surface of the opening as a hydrophobic sealant 5 for the purpose of improving the quality of the seal when the extrusion plunger was inserted and engaged. An electromagnetic radiation-curable ink was then offset coated or screen printed on that portion of the outwardly facing surface of the cartridge body la that would encompass the moisture-curable sealant A.
[0036] Measurement of the moisture permeability
The test specimen for evaluating moisture permeability was prepared by cutting out a sample from cartridge body la on which the electromagnetic radiation-curable epoxy compound based composition 6 had been coated and cured, flattening this sample into a 1.2 mm-thick sheet by means of a hot press at 120°C, and cutting the sheet into a disk with a diameter of 64 mm. Using this test specimen on which the particular electromagnetic radiation-curable epoxy compound based composition 6 had been coated and cured, the moisture permeability was measured by JIS Z 0208, "Test methods for determination of the water vapor transmission rate of moisture proof packaging", by holding for 48 hours in a 40°C/90% RH ambient.
[0037] Preparation of the moisture-curable silicone sealant and ageing procedure An alcohol-eliminating moisture-curable silicone sealant was prepared by mixing the following to homogeneity at room temperature and degassing: 50 parts by weight dimethylhydroxysiloxy-endblocked polydimethylsiloxane (viscosity at 25°C = 17,000 mPa.s), 50 parts by weight calcium carbonate (produced by precipitation, BET specific
2 surface area = 18 m /g, surface treated with fatty acid), 3.0 parts by weight methyltrimethoxysilane, and 1.0 parts by weight di(isopropoxy)titanium di(ethyl acetoacetate). This silicone sealant was filled into the above-described cartridge bodies la. Sealing was then carried out by engaging an extrusion plunger 2 (wall thickness = 1.1 mm), produced by the injection molding of the same high-density polyethylene as used to produce the cartridge body la, into the opening in the cartridge body la. The resulting silicone sealant-filled cartridges 1 were held for 2, 4, 8, 12, 16, or 20 weeks under accelerated ageing conditions (40°C/90% RH). The tests described below were run on cartridges after each ageing period to inspect for the presence of cured material and foaming.
[0038] Inspection for cured material The silicone sealant, after it had been held under accelerated ageing conditions for the prescribed period of time as noted above, was extruded from the cartridge 1 and was visually inspected for the occurrence of microfine cured material.
[0039] Inspection for foaming A joint was set up by placing two strips of backup material (width x length x height = 12 mm x 50 mm x 6 mm) in parallel 12 mm apart on a glass test panel (50 mm x 50 mm x 5 mm). This glass test panel was placed in a 50°C oven and removed after 24 hours and silicone sealant, held for the specified period of time under the conditions described above, was immediately applied into the joint and finished with a spatula. The silicone sealant was subsequently cured by standing for 7 days in a 25°C/50% RH ambient. The occurrence of bubbles between the silicone sealant and glass test panel was then investigated.
Example 1
[0040] An ultraviolet-curing epoxy compound based composition (FDSS 46 Medium from Toyo Ink Mfg. Co., Ltd.) was offset coated on the outer surface of a cartridge body followed by curing by exposure to ultraviolet radiation from a metal halide lamp (output = 80 W/cm) at a transport rate of 15 m/min. The moisture permeability of the resulting cartridge was examined, while the storage stability of the moisture-curable silicone sealant filled into the cartridge was investigated under accelerated ageing conditions. The cured film thickness was 3 μm. The results are reported in Table 1 below.
Example 2
[0041] A cartridge was prepared by carrying out the following process twice: offset coating the outwardly facing surface of the cartridge body with an ultraviolet-curing epoxy compound based composition (FDSS 46 Medium from Toyo Ink Mfg. Co., Ltd.) followed by curing by exposure to ultraviolet radiation from a metal halide lamp (output = 80 W/cm) at a transport rate of 15 m/min. The moisture permeability of the resulting cartridge was examined as in Example 1, while the storage stability of the moisture-curable silicone sealant filled into the cartridge was investigated under accelerated ageing conditions as in Example 1. The cured film thickness was 10 μm. The results are reported in Table 1 below.
Example 3
[0042] An ultraviolet-curing epoxy compound based composition (FDSS 46 Medium from Toyo Ink Mfg. Co., Ltd.) was screen printed on the outer surface of the cartridge body followed by curing by exposure to ultraviolet radiation from a metal halide lamp (output = 80 W/cm) at a transport rate of 15 m/min. The moisture permeability of the resulting cartridge was examined as in Example 1, while the storage stability of the moisture-curable silicone sealant filled into the cartridge was investigated under accelerated ageing conditions as in Example 1. The cured film thickness was 30 μm. The results are reported in Table 1 below. Example 4
[0043] An ultraviolet-curing epoxy compound based composition (FDSS 210 Medium from Toyo Ink Mfg. Co., Ltd.) was screen printed on the outer surface of the cartridge body followed by curing by exposure to ultraviolet radiation from a metal halide lamp (output = 80 W/cm) at a transport rate of 15 m/min. The moisture permeability of the resulting cartridge was examined as in Example 1, while the storage stability of the moisture-curable silicone sealant filled into the cartridge was investigated under accelerated ageing conditions as in Example 1. The cured film thickness was 20 μm. The results are reported in Table 1 below.
Example 5
[0044] An ultraviolet-curing epoxy compound based composition (UN POL 310 from
Teikoku Printing Inks Mfg. Co., Ltd.) was screen printed on the outer surface of the cartridge body followed by curing by exposure to ultraviolet radiation from a metal halide lamp (output = 80 W/cm) at a transport rate of 15 m/min. The moisture permeability of the resulting cartridge was examined as in Example 1, while the storage stability of the moisture-curable silicone sealant filled into the cartridge was investigated under accelerated ageing conditions as in Example 1. The cured film thickness was 20 μm. The results are reported in Table 1 below.
Comparative Example 1
[0045] Cartridge production was carried out as in Example 1, but in this case without application of the electromagnetic radiation-curable epoxy compound based composition on the cartridge. The moisture permeability of the resulting cartridge was examined as in
Example 1, while the storage stability of the moisture-curable silicone sealant filled into the cartridge was investigated under accelerated ageing conditions as in Example 1. The results are reported in Table 1 below. Table 1.
Abbreviations used: CM cured material
F foaming
J--
Example 6
[0046] An ultraviolet-curing epoxy compound-based composition (DAICURE RT-7 from
Dainippon Ink And Chemicals Inc.) was offset coated on the outwardly facing surface of the cartridge body followed by curing by exposure to ultraviolet radiation from a metal halide lamp (output = 80 W/cm) at a transport rate of 15 m/min. The moisture permeability of the resulting cartridge was examined as in Example 1, while the storage stability under accelerated ageing conditions as in Example 1. The Cured film thickness was 3 um. The results are reported in Table 2 below. It should however be noted that in the case of Daicure
RT-7 the main-component is trimethyrolpropanetriacrylate and sub-component is bisphenol epoxy resin whereas the main component in the other inks used in examples 1 to 5 are bisphenol epoxy resins and as such the results in example 6 are not as good as those in examples 1 to 5.
Comparative Example 2 [0047] A heat-curing urethane compound-based composition (SS PO Medium from Toyo Ink Mfg. Co., Ltd.) was screen printed on the outwardly facing surface of the cartridge body followed by curing by heat at a temperature of from 80 to 90° C for 5 min. The moisture permeability of the resulting cartridge was examined as in Example 1, while the storage stability under accelerated ageing conditions as in Example 1. The cured film thickness was 5 um. The results are reported in Table 2 below.
Table 2.
Abbreviation used: CM = cured material F = foaming
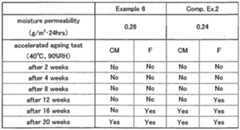
Industrial Application [0048] The moisture-curable sealant cartridge according to this invention is characterized by an excellent moisture barrier performance and by the fact that it enables the long-term storage of moisture-curable sealant filled therein. These characteristic features accrue because an electromagnetic radiation-curable epoxy compound-based composition is coated and cured on at least that portion of the cartridge body that encompasses or holds the moisture-curable sealant. The moisture-curable sealant-filled cartridge according to this invention, which comprises the aforesaid moisture-curable sealant cartridge filled with moisture-curable sealant, is characteristically able to provide good usability due, even after long-term storage, to the absence of foaming by the sealant and the absence of production of cured material within the cartridge. The inventive method for producing the cartridge body for application with moisture-curable sealants is characterized by coating an electromagnetic radiation-curable epoxy compound-based composition on a cylindrical polyolefin cartridge body followed by curing by exposure to radiated active energy. This method therefore enables the highly efficient and inexpensive production of the described cartridge body.