スズキ車のMT製造工場が挑む生産革新
MC1台に工程集約
スズキ部品製造(浜松市浜名区、金原裕之社長)は、スズキグループで、主に4輪車、2輪車・船外機の駆動系部品、足回り部品を生産する。浜松市内に3つの工場を構え、アルミニウムダイカストから機械加工、組み立てまでの一貫生産体制を敷く。本社工場と位置付け、主にスズキ車の手動変速機(MT)を生産するスズキ部品浜松工場(同区)では設備のセル化による多品種少量対応など生産革新に挑んでいる。(浜松支局長・本荘昌宏)
スズキ部品浜松工場はアルミダイカストから穴開けなどの切削加工、シャフトやギア部品の組み込み工程を行っている。スズキ車の国内生産分のMTのケースの大半を製造しており、変動はあるものの生産規模は「おおむね月に10万台分」(金原社長)という。出荷先の多くはスズキの国内工場だが、一部海外工場や外部企業にも納めている。
ダイカスト工程では受け入れたアルミのインゴット(塊)を溶解炉で溶かして、金型に投入、鋳造する。溶解炉には断熱塗料や断熱シートによる放熱対策を施し、省エネルギーや作業環境の向上に取り組んでいる。
鋳造品は機械加工工程では、組み立て時に過度な隙間ができないように仕上げる技術が特徴。別拠点のスズキ精密工場(同区)で製造したギアなど関連部品を組み込み、MTのケースなどとして出荷する。
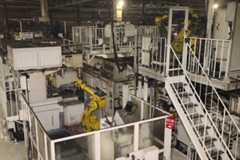
生産管理の方針として「まずは能率を出すようにしている」(同)という。例えば定時前に生産が終わっても「定時内でダラダラと仕事を続けるよりいいと考える」(同)。その場合、残りの時間分で人員をどのように別工程に振り向けられるかが重要になる。
工場設備はやや老朽化しているため、更新投資が課題だ。車の電動化が進むにつれ、数量が減る部品も出てくる状況下で、今後は多品種少量生産に対応できる汎用的な設備が必要になる。
設備はさまざまな装置を直列に配置した、いわゆるライン形式が多い。少品種大量生産には適しているが、多品種少量生産しようとすると設備が多い分、段取りが煩雑になる。そこで取り組んでいるのが設備のセル化だ。
例えば、複数の設備を用いていた工程を1台のマシニングセンター(MC)に置き換える。1個当たりの所要時間は増えるが、生産量の負荷に応じてセルを増やし、生産しない時にはセルを止めるといった柔軟な生産体制を築く。
工程集約により設備が減ると、工場内には空きスペースが生まれる。そうした区画を新たに電気自動車(EV)部品の生産などに活用していく考えだ。